Taking Full Advantage Of Effectiveness and Quality With Cutting-Edge Metal Stamping Approaches
In the world of steel marking, the pursuit of operational excellence through the integration of cutting-edge techniques is paramount. As sectors evolve and demands for accuracy and performance rise, staying in advance of the contour ends up being a calculated crucial. By accepting cutting-edge technologies and process enhancements, organizations can open brand-new levels of productivity and item top quality. The junction of advanced metal stamping techniques, automated systems, stringent top quality controls, and lean manufacturing concepts uses an alluring glance right into the future of manufacturing. This convergence holds the pledge of not just meeting but exceeding market standards, setting the stage for unrivaled performance and client complete satisfaction.
Advanced Metal Stamping Technologies
In the world of steel marking, the assimilation of sophisticated technologies has revolutionized the industry, boosting accuracy and efficiency in manufacturing procedures - Metal Stamping. Advanced steel stamping modern technologies have played a pivotal role in raising the capacities of makers, enabling more complex styles and higher manufacturing rates
Among the most substantial innovations in metal stamping innovation is the execution of computer system numerical control (CNC) systems. CNC systems enable exact control over the marking procedure, causing accurate and consistent manufacturing of complicated parts. In addition, the usage of servo presses has actually caused improvements in energy performance and lowered cycle times, better optimizing the production procedure.
Furthermore, the integration of automation and robotics has structured metal marking operations by increasing productivity and lowering the risk of mistakes. Automated systems can carry out tasks with speed and precision, bring about enhanced general effectiveness in the assembly line.
Automated Processes for Effectiveness
Use of automated processes in metal stamping operations has actually substantially improved performance and performance in manufacturing centers (Metal Stamping). Automated systems have actually transformed the metal marking sector by streamlining processes, lowering hand-operated treatment, and reducing the margin of error. These automated remedies include a series of modern technologies, including robotic arms, CNC machines, and digital control systems, that job cohesively to implement detailed marking jobs with accuracy and rate
One primary benefit of automated procedures in steel stamping is the constant quality they provide. By removing human mistake and variations in production, automated systems make sure that each stamped component fulfills exact requirements with marginal issues. Furthermore, automation makes it possible for constant procedure, significantly reducing downtime for tool changes and maintenance, consequently making best use of overall productivity.
Furthermore, automated procedures improve safety in metal stamping procedures by decreasing the need for hand-operated handling of sharp devices and hefty materials. This not only safeguards workers but also adds to a more effective and streamlined process. Finally, the combination of automated processes in steel marking procedures is important for attaining ideal efficiency, top quality, and safety criteria in modern manufacturing environments.
Quality Control Actions in Marking
Given the focus on regular quality and effectiveness accomplished with automated procedures in steel stamping operations, carrying out durable quality control steps ends up being vital to ensure and support criteria precision in stamped components. Quality control in metal marking entails a multi-faceted strategy to assure the integrity and accuracy of the final items. By integrating these measures right into steel stamping operations, manufacturers can regularly create high-grade stamped parts that satisfy the rigorous demands of modern-day sectors.
Enhancing Accuracy With Development
To attain unparalleled precision in steel marking processes, pioneering advancements are continuously being established and integrated right into the production process. Advanced innovations such as laser reducing systems and computer numerical control (CNC) equipments have actually transformed the means steel elements are marked with utmost accuracy. By making use of laser cutting technology, manufacturers can accomplish complex and elaborate designs with micron-level precision, making certain that each stamped part meets the strictest quality requirements.
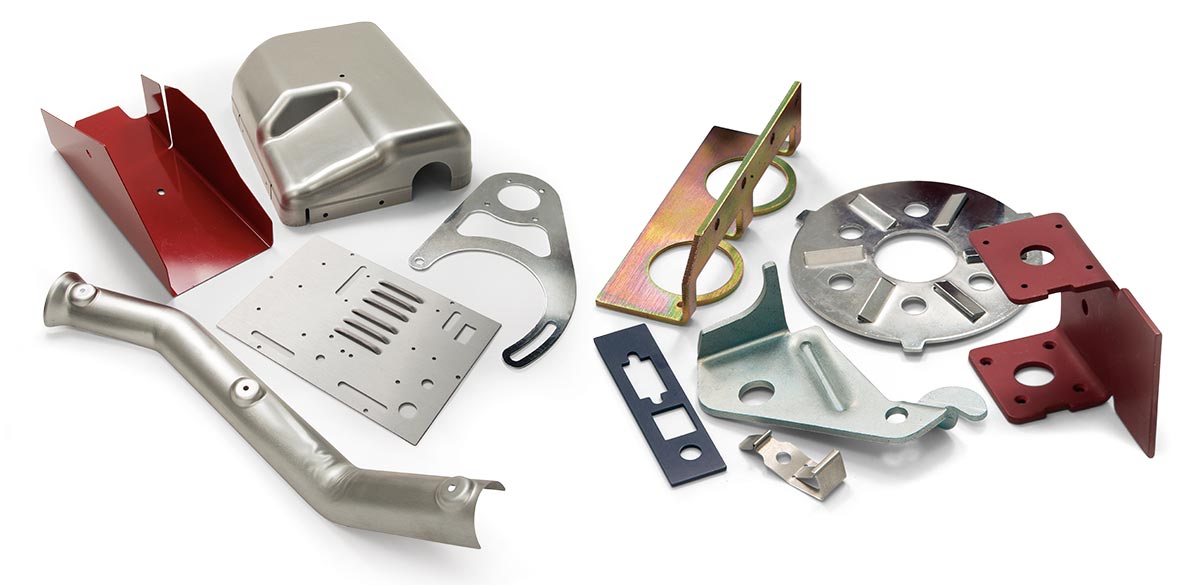
Furthermore, making use of simulation software application permits suppliers to evaluate and enhance stamping processes before real production, recognizing possible areas for improvement and fine-tuning criteria to accomplish my website maximum precision. By accepting these cutting-edge innovations, suppliers can enhance precision, increase efficiency, and provide premium stamped products that fulfill one of the most stringent requirements of modern sectors.
Carrying Out Lean Manufacturing Practices
Incorporating lean manufacturing techniques right into metal marking operations can cause structured production procedures and increased total performance. By concentrating on getting rid of waste, enhancing resources, and continuously improving procedures, steel stamping companies can improve efficiency and quality while minimizing costs. One vital element more info here of carrying out lean manufacturing in steel stamping is the focus on creating a effective and smooth process. This entails arranging workstations, standardizing processes, and decreasing unnecessary activities to make best use of efficiency.
Furthermore, lean production practices encourage a culture of continuous renovation within the organization. By equipping workers to determine and resolve inadequacies, firms can make step-by-step changes that cause substantial productivity gains with time. Implementing devices such as five, Kanban systems, and worth stream mapping can assist simplify operations, lower preparations, and boost general quality in steel marking procedures.
Conclusion
Finally, the utilization of sophisticated metal marking technologies, automated procedures, high quality control steps, development for accuracy improvement, and implementation of lean manufacturing methods are essential for maximizing efficiency and quality in metal stamping procedures. These methods ensure that items are generated with precision, consistency, and cost-effectiveness. By incorporating these advanced techniques, makers can stay competitive in the sector and fulfill the demands of consumers properly.
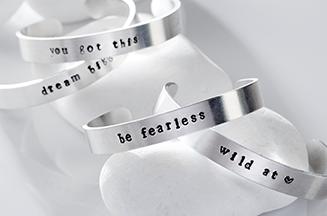
Provided the focus on consistent high quality and effectiveness accomplished through automated processes in steel marking procedures, applying Related Site durable high quality control measures ends up being crucial to guarantee and support requirements precision in stamped components. Executing tools such as 5S, Kanban systems, and value stream mapping can aid improve operations, decrease lead times, and boost total quality in metal marking procedures.
In verdict, the usage of sophisticated metal stamping innovations, automated processes, high quality control steps, development for accuracy improvement, and application of lean manufacturing practices are critical for making the most of effectiveness and high quality in steel marking procedures.